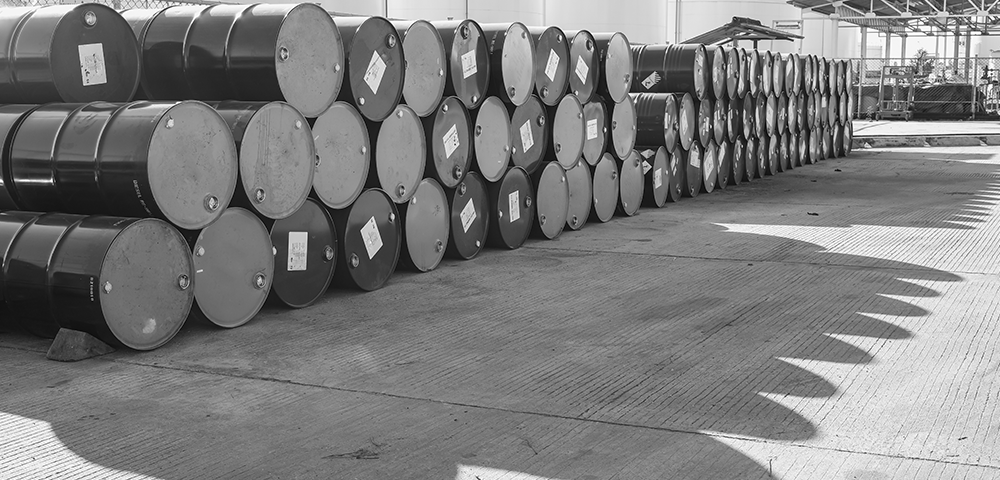
/ IN THIS BLOG
As manufacturing wastes can include a wide variety of substances, both hazardous and non-hazardous, you need to analyze the different types of raw materials that go into your manufacturing processes in order to find ways to reduce hazardous waste management costs.
01 / What's considered manufacturing waste (aka industrial waste)?
There are generally three kinds of waste that manufacturers need to manage: municipal wastes, industrial wastes, and hazardous wastes.
Municipal wastes. The least troublesome of industrial wastes are officially called “municipal solid wastes,” but more colloquially “trash” or “garbage.” This is the kind of waste that garbage trucks routinely pick up in front of homes, schools, hospitals, and businesses. E.g., product packaging, furniture, clothing, bottles, food scraps, newspapers, etc.
Industrial wastes (aka manufacturing wastes). These include a wide variety of non-hazardous materials that are useless, unwanted byproducts of manufacturing. These are not hazardous wastes, which are endemically dangerous or harmful to human health or the environment. As such, industrial wastes don’t require hazardous waste management. Nonetheless, they might require special handling per the EPA, OSHA, DOT, or some state or local authority.
Hazardous wastes. These are a complicated topic in and of themselves. Suffice to say that something must be “listed,” “acutely hazardous,” or “characteristic” to be considered an intrinsically hazardous waste, and therefore in need of RCRA-compliant hazardous waste disposal. Otherwise, it’s probably an industrial waste or (less likely) a municipal one.
02 / How can you reduce manufacturing waste volumes?
Measure your waste streams. Knowing the categorical amounts of industrial, hazardous, and municipal waste you’re generating is logically the first step in reducing the amounts of each.
Your waste hauler can provide numbers in terms of pounds per pickup. Or, if you’re using front-loading bins, you can conduct “bin audits” before each pickup to estimate the total cubic yards that you’re disposing of.
It’s also important to know how much each department in your manufacturing facility is contributing to your three waste streams (e.g., warehousing, offices, food services, grounds, construction, manufacturing, vehicle maintenance, etc.).
Once you know how much waste you’re generating and from where, your managers and/or key employees can set goals for reducing the quantities by some reasonable percentage.
Analyze your waste streams. This involves separating and measuring individual waste streams to determine how the materials in each might be reduced, reused, repurposed, or recycled. Any amount of materials you can divert from a waste stream into a recycling program commensurately reduces the disposal costs for that waste stream. This benefits you in four ways:
- Reducing the amount of waste is primary to reducing your waste management costs.
- Ensuring that wastes are categorically separated keeps municipal and industrial wastes out of your hazardous waste stream, where both would spuriously increase its volume and thus your hazardous waste disposal costs.
- Waste reduction contributes to your efforts at sustainability: something that’s good for your brand image as well as for the environment.
- Materials that can be reused or repurposed, of course, reduce your acquisition costs for raw materials. And those that you can’t reuse or repurpose yourself can be sold, providing a new revenue stream. (I.e., your waste might be another company’s resource.)
Quantify your organic-waste generation. This is another possible component of waste-stream analysis. Even if you have no organic waste that’s a byproduct of your manufacturing, consider food waste traceable to your cafeterias and breakrooms. You might want to hire an organics recycling service. Some states are now (or soon to be) requiring businesses that generate significant amounts of organic wastes to do so.
Train your managers and employees. You can’t merely suggest to managers and employees that they become more thoughtful about what they dispose of and where they put it. A waste reduction program won’t work unless it’s formalized, employees are well informed about it, and there are incentives for compliance (and, perhaps, disincentives for noncompliance). This requires employee meetings, company newsletters, incentive programs, and similar human-resource strategies.
Invest in signage. Everyone needs reminders. Signage provides them. For example, people are less likely to throw wastepaper into a general waste bin if there’s a blue one next to it with a sign above it, reminding them to recycle paper. Likewise, an aluminum recycling bin next to the soda machine, with a recycling sign above it, decreases the chances that cans will wind up in the general trash.
Also, signage placed throughout your facility that generally promotes recycling and waste reduction can help instill those values into your internal business culture, greatly increasing acceptance and compliance for your manufacturing-waste reduction efforts.
03 / Where can you find help to reduce manufacturing waste?
A reputable hazardous waste management provider—by assessing how you generate waste and the materials themselves—can help you develop ways to reduce waste streams, as well as distinguish among industrial wastes that require hazardous waste disposal vs. those that don’t, thereby reducing your manufacturing-waste disposal costs.
MCF Environmental Services is dedicated to providing simple, affordable, sustainable solutions to manufacturers so that they can reduce waste streams with minimal impact on their day-to-day operations.
We take a “partnering” approach to offer you unsurpassed waste management expertise in such matters as:
Choosing the optimal dumpster(s) for your size of plant or factory
Supplying specific kinds of waste and recycling bins for smooth onsite transit & handling of waste
Recommending specialized equipment for your particular kind(s) of waste stream(s)
Developing recycling programs that allow you to reuse and/or repurpose manufacturing byproducts
Robert Losurdo
President, COO