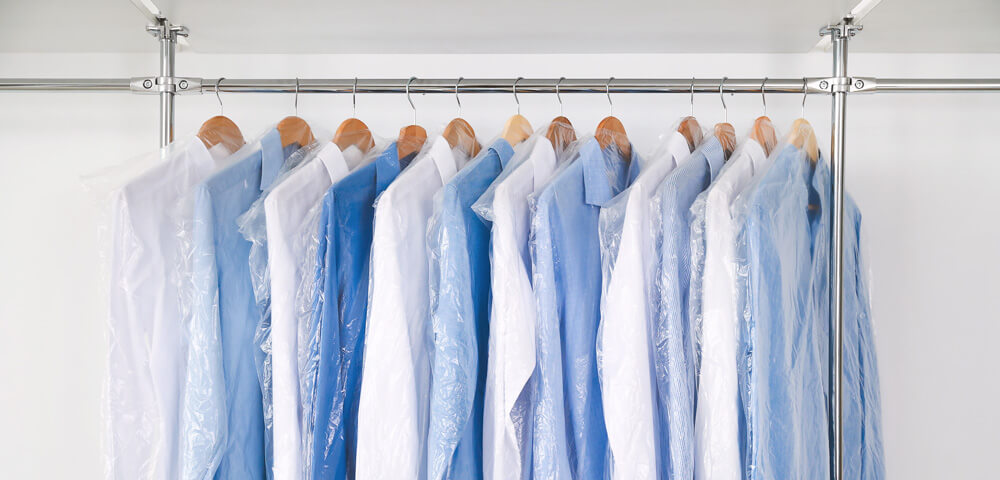
/ IN THIS BLOG
The most common hazardous chemical dry cleaners use is the solvent perchloroethylene (PERC). But there are many other chemicals which have the potential to damage the environment and/or negatively impact people’s health. Because the contaminants that result from dry cleaning operations can be harmful, it’s essential for dry cleaning businesses to comply with the regulations of the Resource and Recovery Act (RCRA).
These regulations were established by the Environmental Protection Agency (EPA) to ensure the safe management of hazardous waste. Familiarizing yourself with these regulations is a critical step to make sure your business stays compliant and keeps your customers, employees, and the public safe from dry cleaning hazardous waste. Dry cleaning disposal can be complicated, so, here we’ll work on breaking it down and simplifying the process so you have a better understanding of dry cleaning RCRA requirements.
01 / Identifying Hazardous Waste
One of the primary requirements of the RCRA is to identify the hazardous waste a business generates. The process follows these three steps:
Obtain an EPA identification number from your state’s hazardous waste agency.
Next, you’ll need to determine if your business generates hazardous waste and is therefore subject to RCRA hazardous waste regulations.
You will also need to identify the types of waste generated and differentiate between chemical waste, solid waste, and used oil. Used oil is subject to different management standards than those for hazardous waste.
Use the enclosed safety data sheets that come with the chemicals and other products you use to learn about their properties. This will help in determining whether the products your dry cleaning business uses and the by-products it generates are hazardous or not.
02 / Determining Your Generator Status
The RCRA requires that dry cleaners calculate the amount of waste their business generates at their location. The waste your business accumulates before it is collected and disposed of is regulated. Additionally, there are regulations covering the way in which the waste is managed and stored.
03 / Standards for a Satellite Accumulation Area
If your business accumulates dry-cleaning hazardous waste within a satellite accumulation area, the regulatory burden is minimal. A satellite accumulation area is at or near the business generating the waste and under its control. If the amount of waste being generated is less than 55 gallons and in the satellite accumulation area, there is no time limit on the accumulation. However, waste accumulated in the satellite accumulation area beyond the 55-gallon limit must be moved from the area within three days.
04 / Standards for Areas That Fail To Meet Satellite Accumulation Requirements
As you can see, there are some benefits from a satellite accumulation space. But what happens if your business’s waste accumulation fails to meet the requirements for such satellite accumulation? In such situations, you’ll be subject to stricter requirements. These requirements vary depending on your generator status.
A large quantity generator (LQG) generates at least 2,200 pounds of hazardous waste per month. Whereas a small quantity generator (SQG) produces at least 220 pounds of hazardous waste per month but less than 2,200 pounds. A very small generator (VSQG) designation is for a business which produces 220 pounds or less of hazardous waste per month.
For LQGs with waste accumulation that does not meet the satellite accumulation requirements, waste can be accumulated for 90 days without a permit. In contrast, SQGs are permitted to accumulate waste for either 180 days or 270 days, depending on whether the hazardous waste will be transported for over 200 miles to reach the destination facility.
You need to count the accumulation time starting when the waste is first generated or when it is removed from the satellite accumulation area. Then, you must place the waste in an exempt area or send it off-site within the appropriate time period. If either an SQG or an LQG fails to remove the waste within the required time period, it will be subject to the requirements of a hazardous waste storage facility unless it obtains an exemption.
05 / Storing and Disposing of Hazardous Waste
It’s important to note that dry cleaning RCRA requirements also cover the storage and disposal of the hazardous wastes your facility generates. Let’s briefly explore the storing and disposal of such waste.
06 / Storing Waste
Waste must be stored in containers that are in good condition. The containers must also remain closed unless you are adding or removing waste and be compatible with the waste being stored. In addition, businesses must also inspect the containers at least once every week to ensure safety and containment of the contents.
LQGs may also have a secondary containment system and can use containers and accumulation tanks if they have been assessed for integrity. These units must be inspected on every operating day. SQGs are also permitted to use certain containers and accumulation tanks, but it’s important to review the requirements for these.
While the type of container is important, so is labeling. All units used by your dry cleaning business to store accumulated waste must be clearly marked with the start date of the accumulation period along with the words “Hazardous Waste.”
Storage facilities are also required to comply with organic air emissions requirements and must be equipped with suitable emergency contingency plans for fire, explosion, and the unplanned release of waste. This plan must be readily available to employees.
07 / Disposing of Waste
Before any waste is transported, copies of the hazardous waste manifest must be prepared and will accompany the waste to the disposal facility. This manifest is a multiple-page form that will document the specific waste's progress through the treatment, storage, and disposal process. This form is obtained from the appropriate state agency. Then, one copy will remain on the premises while others will accompany each transporter. Additionally, a final copy will go to the destination facility.
These destination facilities must be licensed and permitted by both state and federal authorities in order to handle hazardous wastes. This ensures that the facility can safely and appropriately treat hazardous constituents using approved technologies to meet treatment standards.
08 / Why Dry Cleaning Businesses Use a Professional Hazardous Waste Management Service
As you can see, it’s crucial to the health and wellbeing of any dry cleaning business to understand the basics of handling hazardous wastes generated in the course of business. However, gaining a detailed understanding of the disposal process can be difficult for many due to the many complex regulations surrounding storage, transportation, and treatment. Many business owners lack the time or regulation expertise to handle such fine print.
Fortunately, by partnering with an experienced hazardous waste management provider like MCF Environmental, you don’t have to. MCF Environmental has decades of experience handling every stage of the dry-cleaning waste disposal process and can help keep your business from incurring costly fines or lawsuits. Protect your business and propel your business to future success by choosing MCF Environmental for your dry cleaning waste and disposal needs.
Robert Losurdo
President, COO